What should I use to lubricate deep groove ball bearings and how often should I lubricate them?
What should I use to lubricate deep groove ball bearings and how often should I lubricate them?
Lubricant selection - don't let the bearing "strike due to thirst"
The lubrication of bearings can reduce
friction and prevent overheating. Generally, the lubricants we commonly use are
divided into two categories: grease and lubricating oil.
1)Grease - "Professional care" of bearings
When choosing grease, we need to consider
the following factors:
Base oil type: Base oils include mineral
oil, synthetic oil, etc. Different base oils perform differently under
different temperatures and loads. For bearings in high temperature and high
load environments, it is more appropriate to choose grease based on synthetic
oil.
Thickener: The type of thickener affects
the structure and working stability of the grease. Common thickeners include
lithium-based and calcium-based greases. Among them, lithium-based greases are
widely used in deep groove ball bearings due to their good mechanical stability
and temperature adaptability.
Additives: Additives can improve the
performance of greases, such as anti-oxidation, anti-corrosion, and anti-wear.
2)Lubricating oil - the "Durex" that flows easily
Compared to grease, lubricating oil has
stronger fluidity and is suitable for deep groove ball bearings that rotate at
high speeds. Lubricating oil can better penetrate the friction surfaces of the
bearing, reducing temperature rise and wear. However, the loss of lubricating
oil requires extra attention, so it is usually used in combination with sealing
design to reduce lubricating oil leakage.
Lubrication frequency - regularly "moisten" the bearings
For bearing lubrication, it is necessary to
select appropriate lubricants, and lubricate and maintain them regularly
according to the usage. Regular lubrication is an important factor to ensure
the long-term and efficient operation of bearings.
1)Influence of environmental factors
High temperature environment: If the
bearing operates in a high temperature environment for a long time, the grease
may lose its effectiveness prematurely. Therefore, for bearings used under high
temperature conditions, the lubrication frequency should be appropriately
increased, and even the grease needs to be refilled every few months.
Humid environment: In a humid or high humidity environment, moisture will promote the aging of the grease and may cause the bearing to rust. In this environment, in addition to replacing the appropriate lubricant, the lubrication frequency also needs to be increased to prevent the lubricant from becoming damp and failing.
High load operation: When working under
high load or heavy load conditions, the wear of the bearing is aggravated and
the lubricant is prone to deterioration. Therefore, in this case, the
lubrication frequency should be increased to ensure that the grease is always
in an ideal state.
2)Working time
For deep groove ball bearings in ordinary
industrial environments, it is generally recommended to lubricate or replace
grease every 5,000 to 10,000 hours. For high-speed bearings, lubrication checks
may be required every 500 to 1,000 hours. Regularly check the lubrication
status of the bearings and replenish or replace the lubricant in time to ensure
the stability and reliability of the bearings.
3)Lubricant "life"
Each lubricant has its "life", after which the lubricant's effectiveness will be greatly reduced, and may even cause damage to the bearing. Therefore, even if there is no obvious abnormality in the bearing, regular replacement of the lubricant is a preventive measure.
Conclusion - Lubrication is the "lifeline" of bearings
Whether it is grease or oil, choosing the
right lubricant and a reasonable lubrication frequency can greatly improve the
service life and operating efficiency of deep groove ball bearings. Mastering
the correct lubrication method and cycle can make deep groove ball bearings
more efficient in their work.
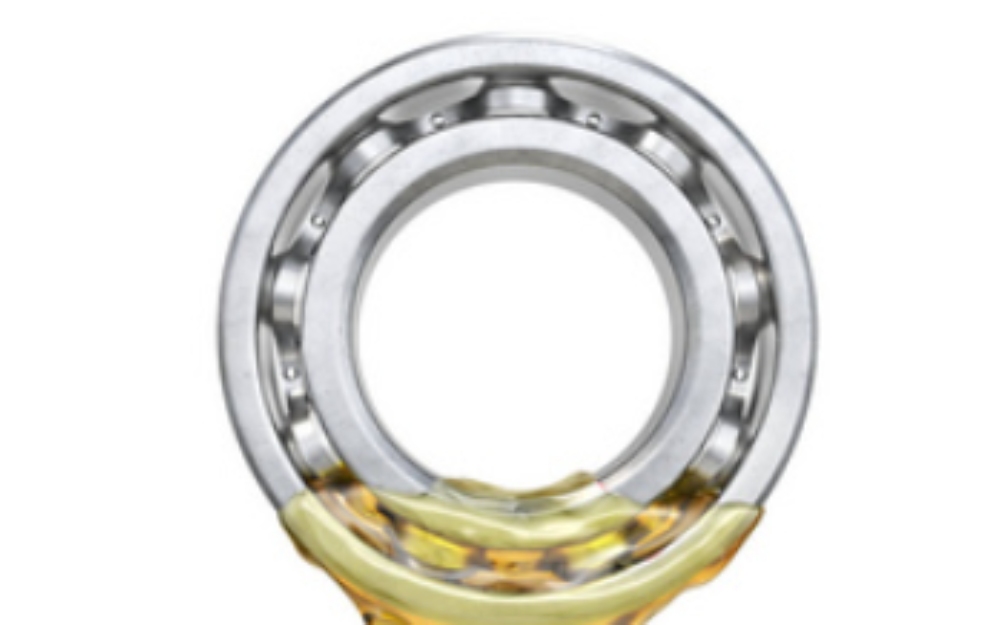
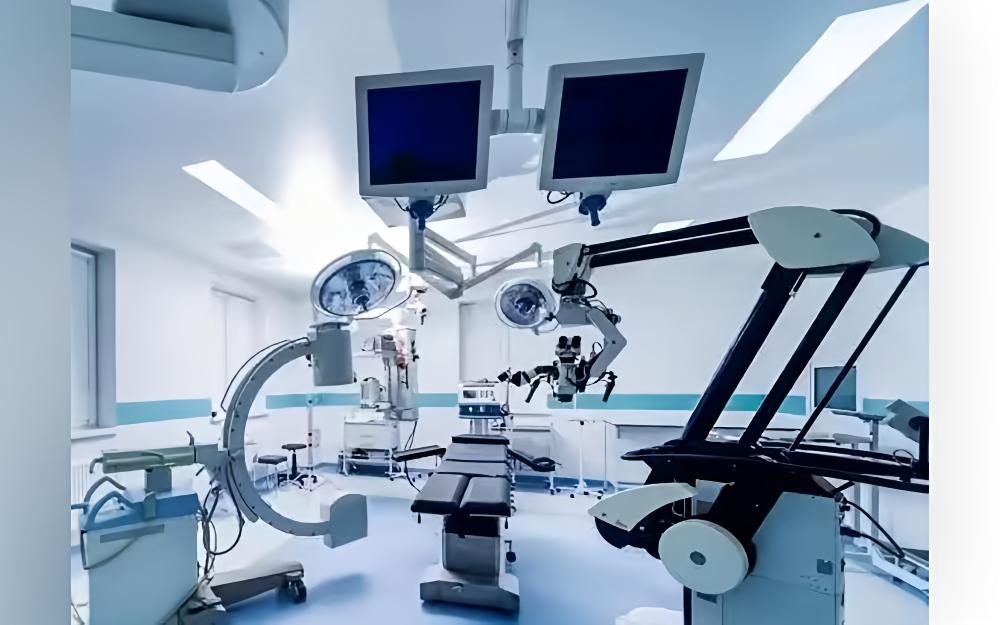
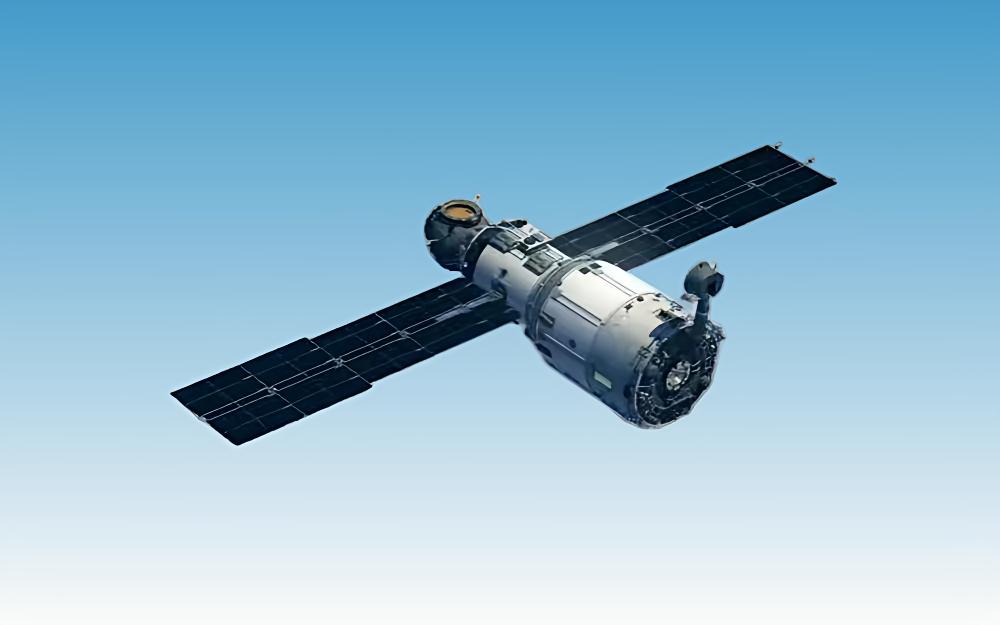